The platinum electrolytic deposition process is an advanced surface treatment used in various industries, particularly aerospace. It involves applying a platinum layer on metallic parts via an electrochemical process. This method is designed to provide superior corrosion protection and is often combined with vapor phase aluminizing (VPA) to enhance the performance of critical components.
Applications
- Engine Components: Used for vanes, stators, turbine blades, compressors, and injectors of turbomachinery, as well as other critical engine components where extending the lifespan of parts in a corrosive environment is essential.
- Maintenance and Repair: Required in maintenance procedures to restore worn parts and extend their lifecycle.
- Performance Enhancement: Treated parts show significant improvement in performance under severe operating conditions.
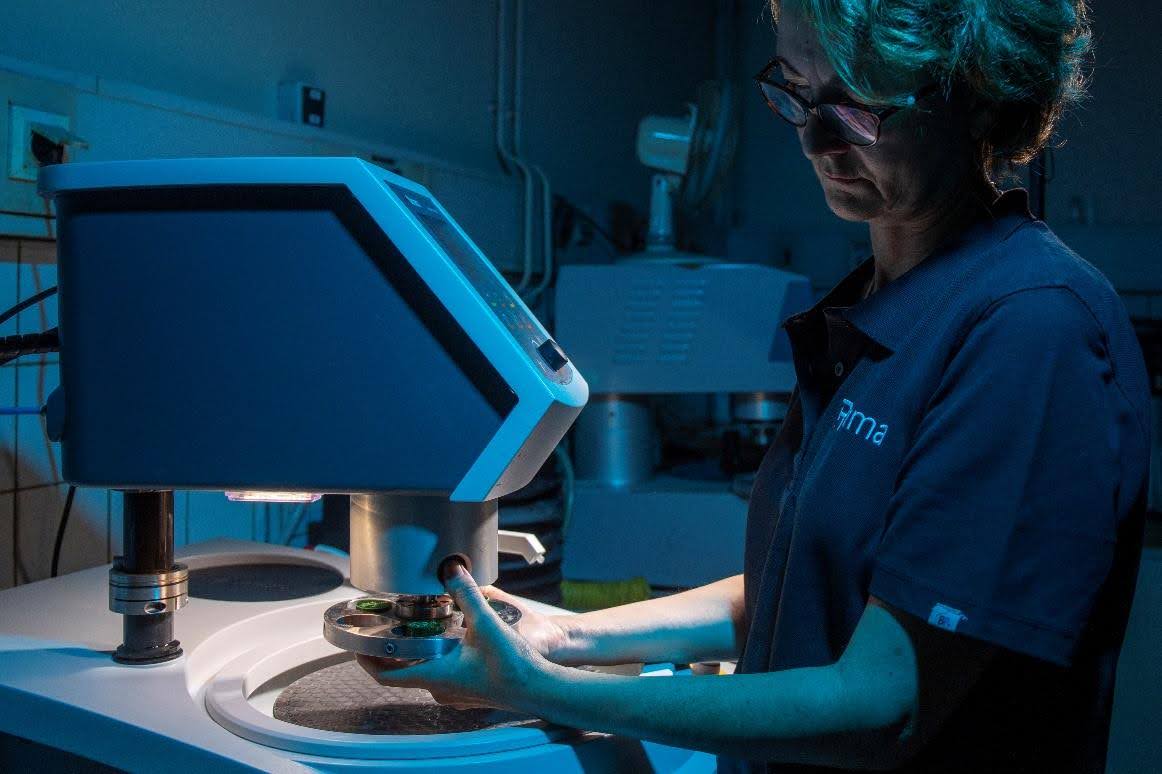
Operating Principles
- Preparation: Parts to be treated are carefully degreased and cleaned to remove any surface contaminants, ensuring optimal adhesion of the coating.
- Masking: Innovative masking solutions are applied to the parts to protect areas that do not require coating. This ensures that the platinum deposition is limited to critical areas, avoiding overspill.
- Immersion: The masked parts are immersed in a bath containing a platinum electrolyte solution. The immersion time and amperage are strictly controlled to ensure a uniform and precise application of the platinum layer.
- Laboratory Control: After deposition, a sample is rigorously inspected in our laboratory to measure the coating thickness, verify its uniformity, and ensure it meets the required specifications.
- Diffusion: The coated parts are then placed in furnaces where the temperature cycle and diffusion time are meticulously controlled to promote optimal platinum diffusion into the material.
- Coupling with VPA: To enhance corrosion resistance, the platinum coating can be combined with a vapor phase aluminizing (VPA) treatment, providing dual protection for components through the creation of a NiPtAl coating.
Advantages of the Process
- Corrosion Resistance: The platinum coating forms an effective protective barrier against corrosive elements, thus extending the lifespan of components.
- Application Flexibility: Thanks to our innovative masking techniques, we can apply the coating selectively, avoiding overspill areas and precisely adhering to specifications.
- NADCAP Certification: Our NADCAP certification ensures that our processes meet the highest standards of the aerospace industry.
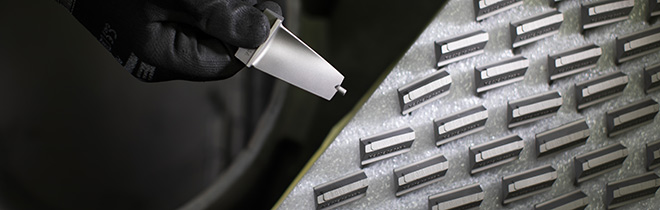