The pack aluminizing process is an advanced surface treatment method used in various industries, particularly aerospace, to deposit aluminium or aluminium-chrome alloy coatings on metallic surfaces. This process involves cement deposition under a controlled atmosphere (hydrogen or argon) followed by high-temperature diffusion to enhance the corrosion and high-temperature resistance of critical components such as turbomachine parts.
Applications
- Engine Components: Used for distributors, turbine blades, compressors, and injectors of turbomachinery, as well as other critical engine components where extending the life of parts in a corrosive environment is essential.
- Maintenance and Repair: Required in maintenance procedures to restore worn parts and extend their lifecycle.
- Performance Enhancement: Treated parts show significant improvement in performance under severe operating conditions.
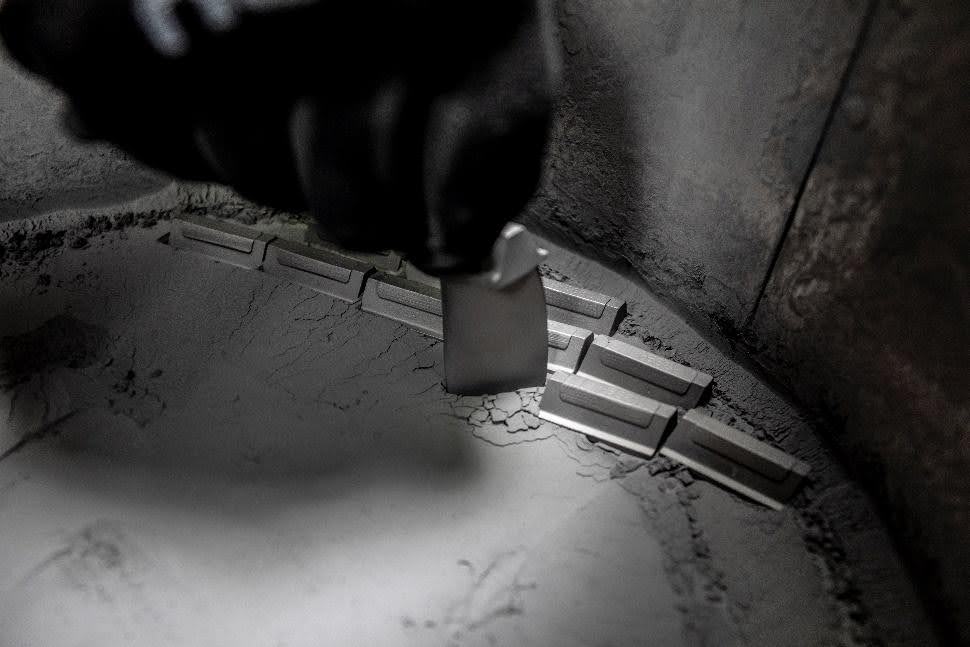
Operating Principles
- Preparation: Parts to be treated are carefully degreased and cleaned to remove any surface contaminants, ensuring optimal adhesion of the coating.
- Masking: Innovative masking solutions are applied to the parts to protect areas that do not require coating. This ensures that the deposition is limited to critical areas, avoiding overspill.
- Aluminizing: The prepared parts are then loaded into a thermochemical furnace where the atmosphere and pressure are strictly controlled. The parts in the furnace are heated to a high temperature (800°C – 1200°C) to promote the evaporation and diffusion of the cement.
- Aluminizing Reaction: The aluminium and/or chrome in the cement evaporates at high temperature and diffuses onto the metal surface, reacting with the base metal to form a protective coating. This coating also diffuses into the material, creating a diffusion zone enriched with aluminium and/or chrome.
- Subsequent Specimens and Destructive Testing: For each treated batch, specimens are included to ensure the quality of the treatment. Destructive testing and coating thickness and uniformity tests are conducted.
- Coloration Tests: Our laboratory conducts coloration tests to evaluate the quality and homogeneity of the coating, ensuring compliance with the required specifications.
Advantages of the Process
- Corrosion Resistance: The coating forms an effective protective barrier against corrosive elements, thus extending the lifespan of components.
- High-Temperature Resistance: Treated parts can withstand high-temperature and highly corrosive environments, increasing their durability and performance.
- Adaptability to Complex Shapes: The treatment is particularly suitable for parts with complex geometries, ensuring complete and uniform coverage.
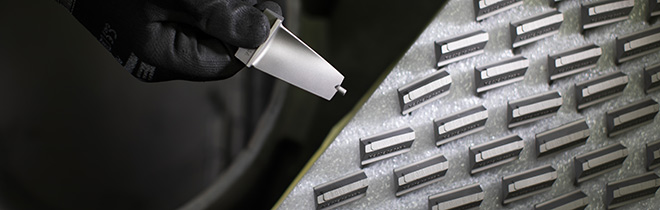