Vapor Phase Aluminizing is a surface treatment method widely used in various industries, particularly in the aerospace sector, to deposit aluminium coatings on metallic surfaces. This process uses aluminum vapor at high temperatures to enhance the corrosion resistance of components such as turbine parts.
Applications
- Engine Components: Used for distributors, turbine blades, compressors, and fuel injectors, as well as other critical engine parts.
- Maintenance and Repair: Used in maintenance processes to restore worn parts and extend their service life.
- Performance Enhancement: Parts treated with VPA show significant performance improvements under severe operating conditions.
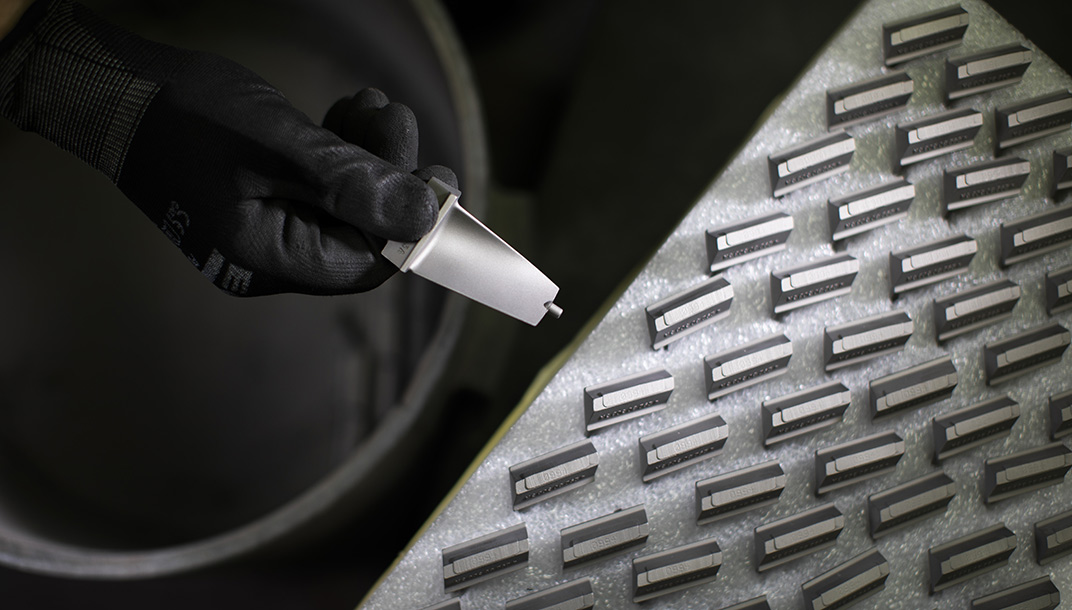
Operating Principles
- Surface Preparation: The metal parts to be treated are first degreased and mechanically cleaned (sandblasting) to remove surface contaminants.
- Loading into the Furnace: The cleaned parts are loaded into a thermochemical furnace where both atmosphere and pressure are strictly controlled.
- Heating: The parts are heated to high temperatures (800°C – 1200°C) to facilitate the evaporation and diffusion of aluminum.
- Aluminizing Reaction: Aluminum vaporizes at high temperatures and diffuses into the metal surface, reacting with the base metal to form a protective aluminum coating. This coating also diffuses into the material, creating a diffusion zone enriched with aluminum.
- Subsequent Testing and Destructive Controls: To ensure the quality of the treatment, mechanical tests and destructive controls are performed to verify the thickness and uniformity of the coating.
- Coloration Tests: Our laboratory conducts color tests to evaluate the coating’s quality and homogeneity, ensuring all required specifications are met.
Advantages of the VPA Process
- Improved Corrosion Resistance: The aluminum coating protects parts against oxidation and corrosion at high temperatures.
- High-Temperature Resistance: Treated parts can withstand extremely high temperatures and corrosive environments, enhancing their durability and performance.
- Adaptability to Complex Shapes: The process is particularly suitable for parts with internal cooling channels, ensuring complete and uniform coverage.
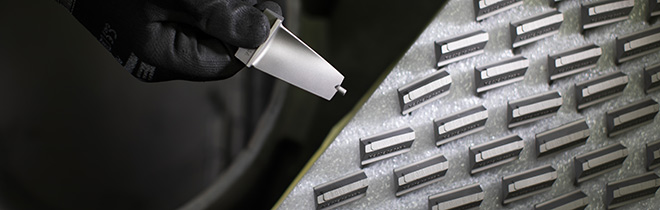